FACTORY SHOW
Tentech operates a spacious factory facility covering over 3,000 square meters, designed to support a wide range of production processes. The area is strategically divided into several zones, including production lines, aging testing, and quality control stations, ensuring efficient workflow and high product standards. The production area is equipped with advanced machinery for precision manufacturing, while the aging testing section is dedicated to evaluating product durability under various conditions. The quality control team rigorously inspects all products, ensuring they meet stringent specifications before reaching customers. This comprehensive setup enables Tentech to deliver reliable, top-quality products consistently.
9 Years+
Since 2015, Professional LED Display Industry Experience
3000+M2
Production Lines, Aging Linesand Quality Control Area
8
Countries Have Factory and Warehouses, Russia, UAE, Egypt, Manila, Kenya, Indonesia, India and Philippine
LED MODULE PRODUCTION LINES
Tentech's LED display factory utilizes advanced automated machinery, including state-of-the-art Surface Mount Technology (SMT) equipment, allowing for precise and efficient placement of LED components onto circuit boards, ultimately guaranteeing the quality and consistency of every produced LED display.
Key Points of Tentech:
Automated Production:
Tentech's factory relies heavily on automated equipment for high-quality and consistent production of LED displays.
SMT Technology:
The key piece of automated equipment mentioned is the Surface Mount Technology (SMT) machine, which precisely places LED components onto circuit boards.
Quality Assurance:
By using advanced SMT technology, Tentech ensures the reliability and consitency of each LED display produced.
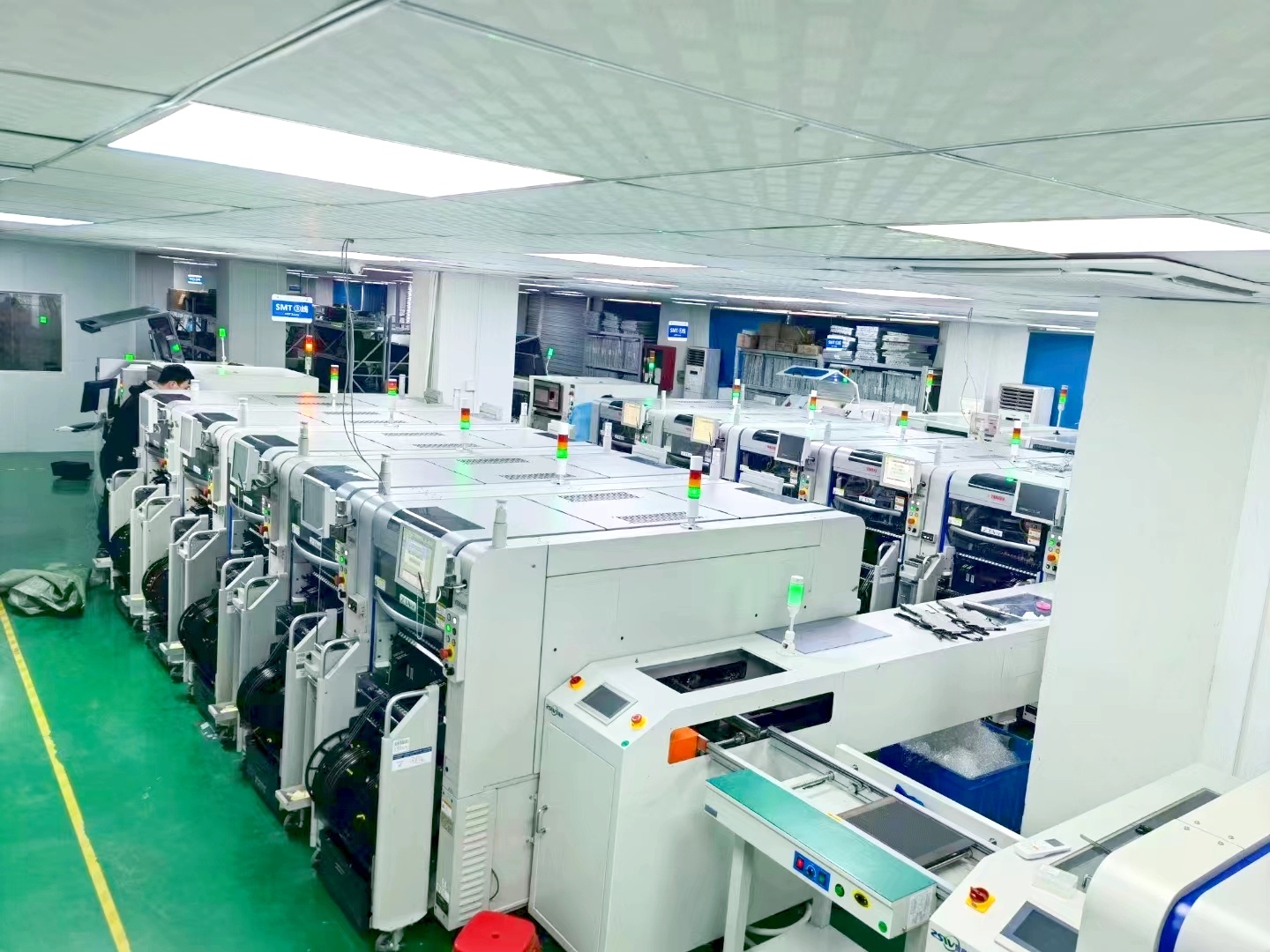
LED SMT
The lamp bead surface requires solder paste application before patching onto the SMT machine. After placement, reinforce the connection during reflow soldering to ensure proper bonding and reliability.
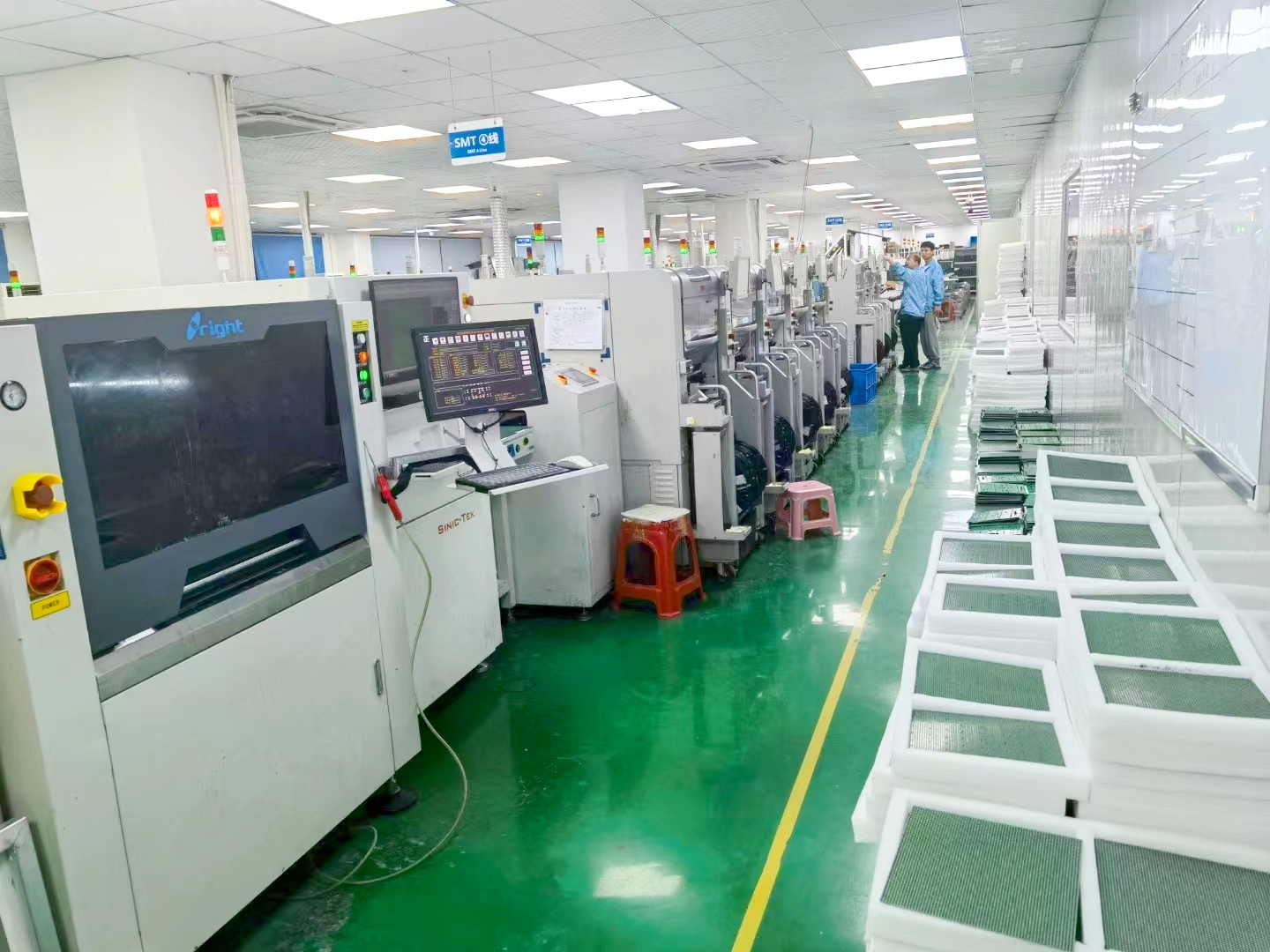
PCB SMT
IC SMT requires first applying solder paste, followed by placing ICs, resistors, capacitors, power sockets, and signal sockets. Finally, components are reinforced through reflow soldering for strong electrical connections.
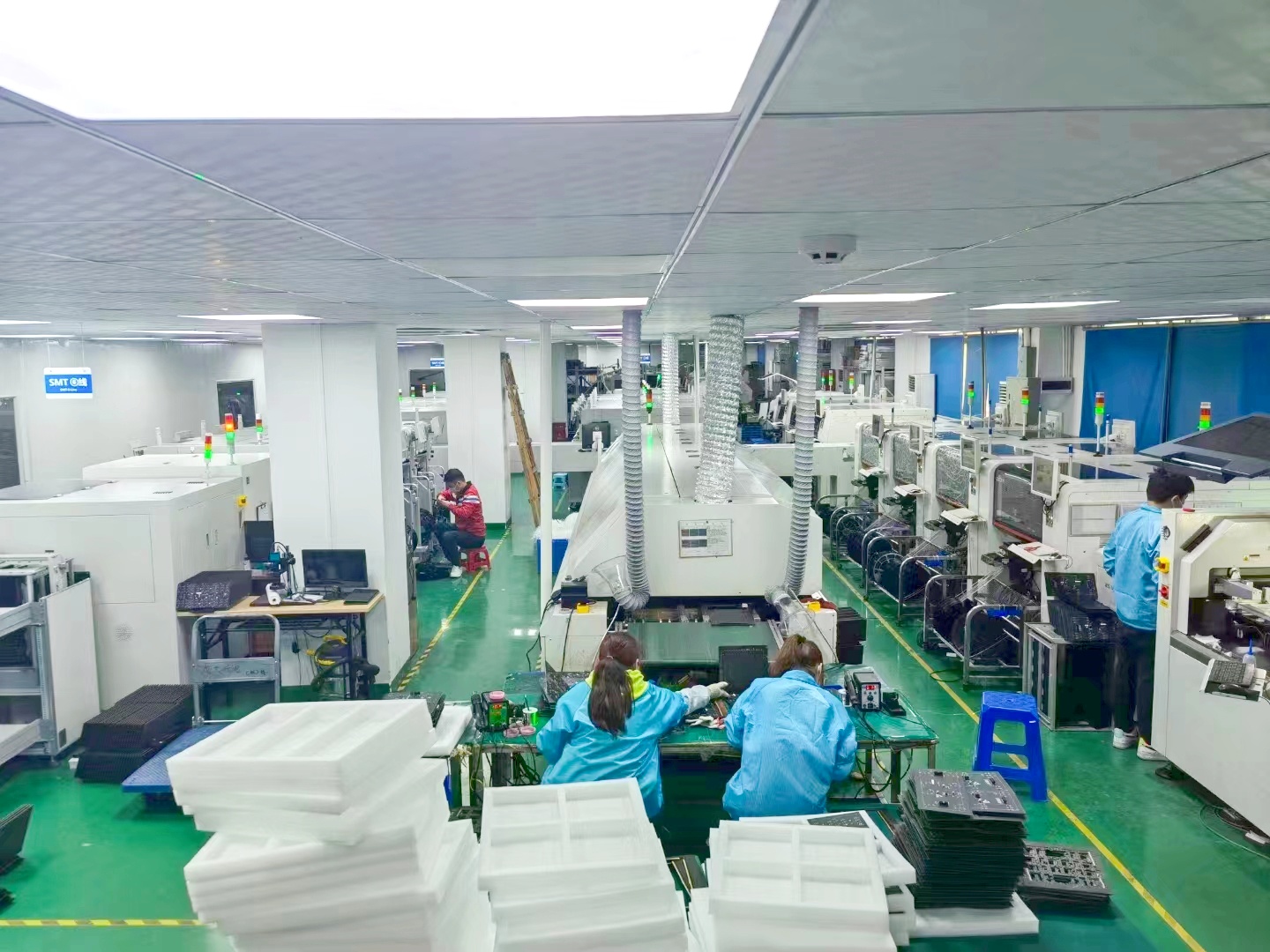
Module SMT
LED module SMT involves soldering surface-mount components (LEDs, resistors, capacitors) onto a PCB using pick-and-place machines, followed by reflow soldering to ensure proper electrical connections and functionality.
ASSEMBLY AND AGING LINES
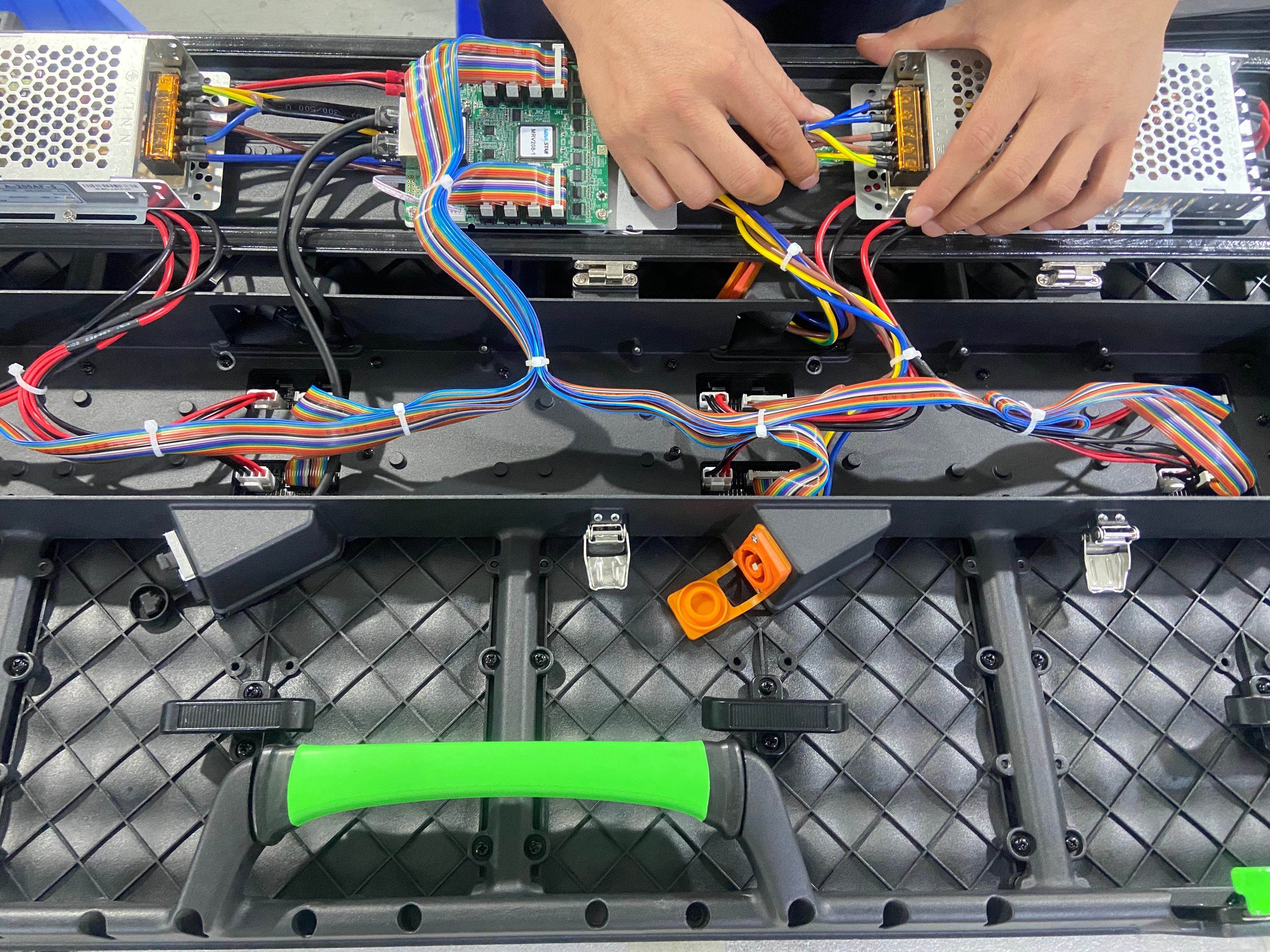
led Display assemble
Professional workers are assembling LED Module, Power Supply, Receiving Card on LED Display cabinet.
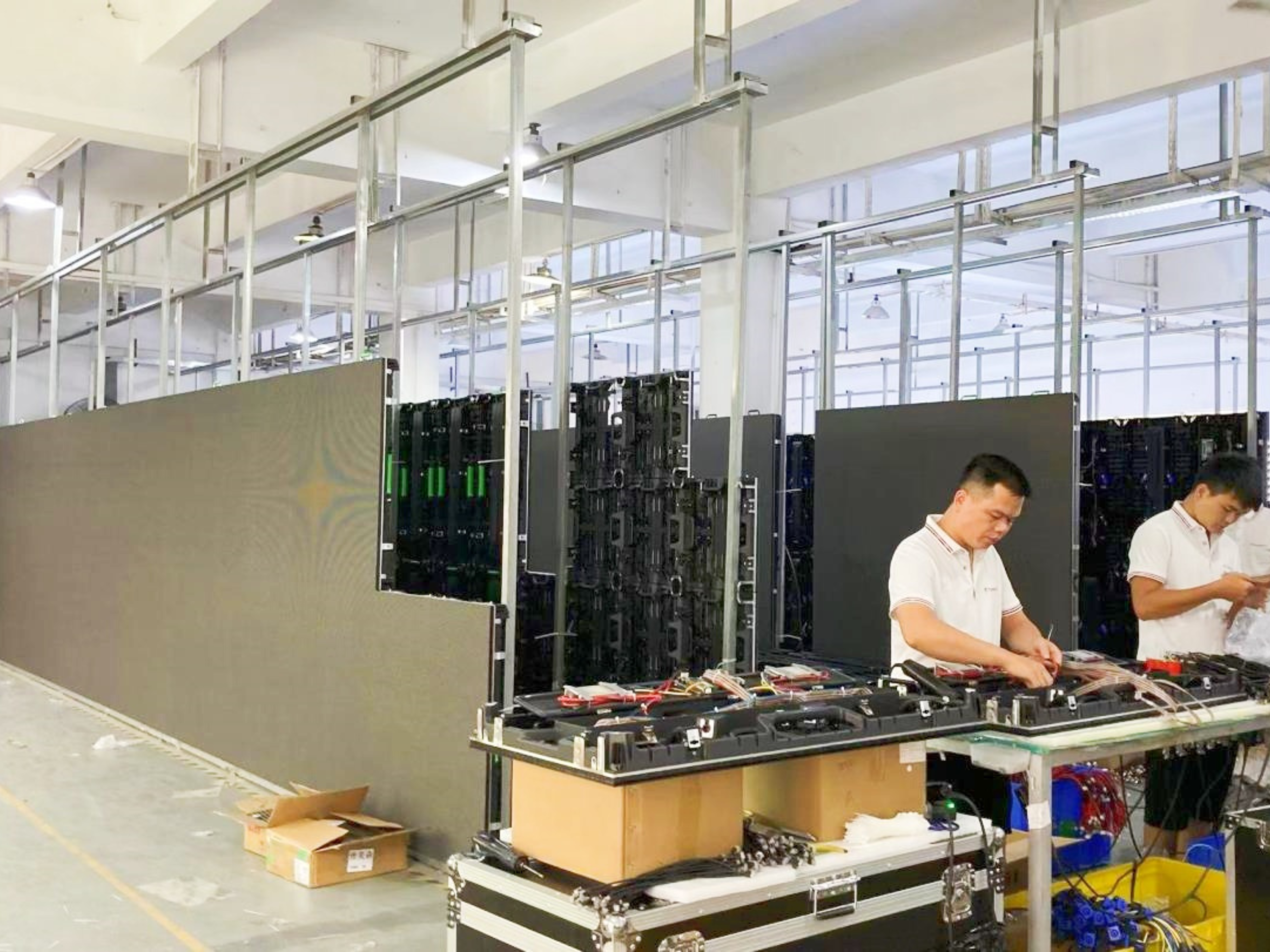
Quality Control Lines
Quality controling is the most importing part before export. Experienced workers are QC checking.
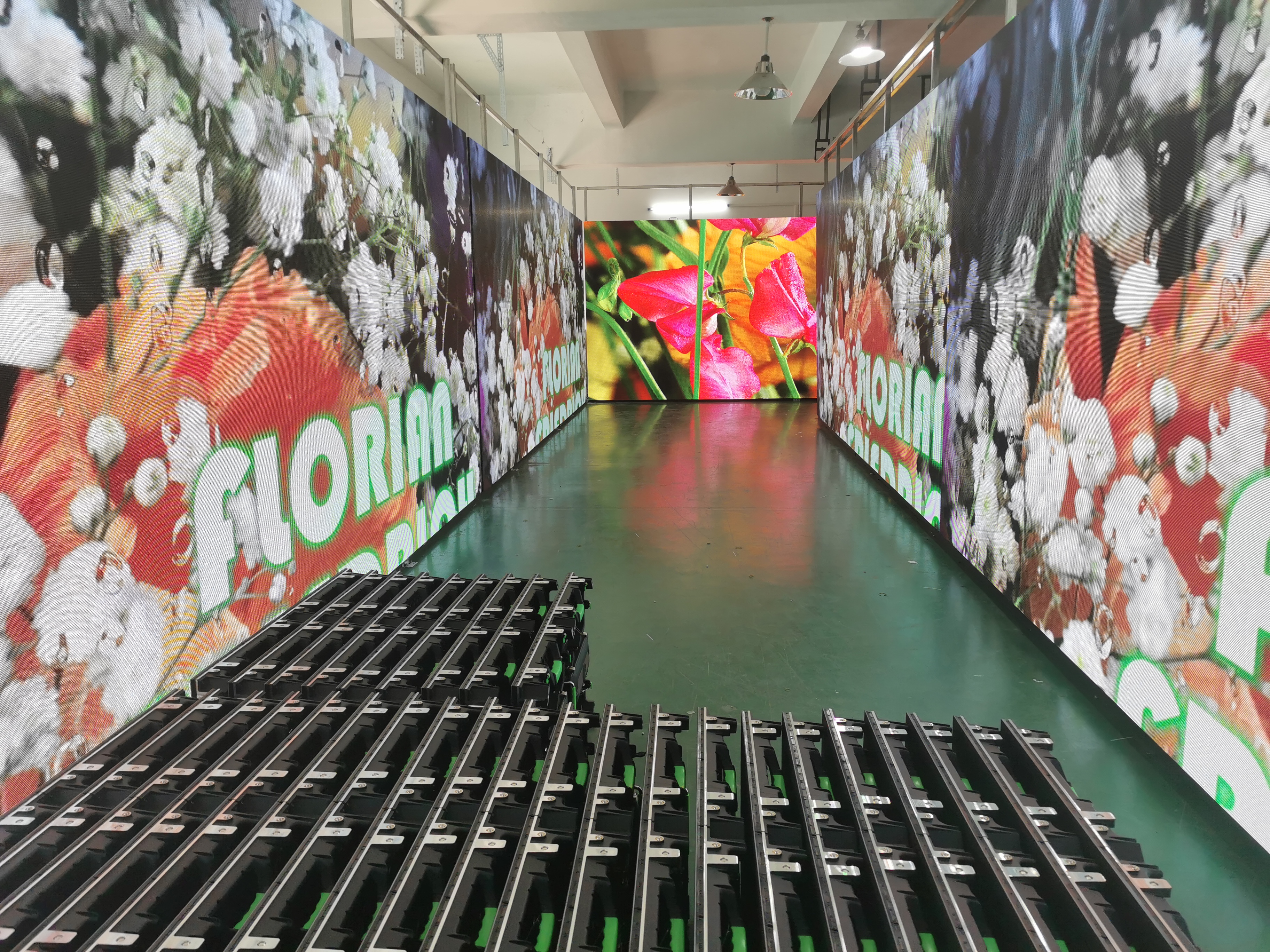
LED SCreen aging
After finishing assebled the cabinets are subjected to an aging testing for 48/72 hours.
Factory's Photo Gallery
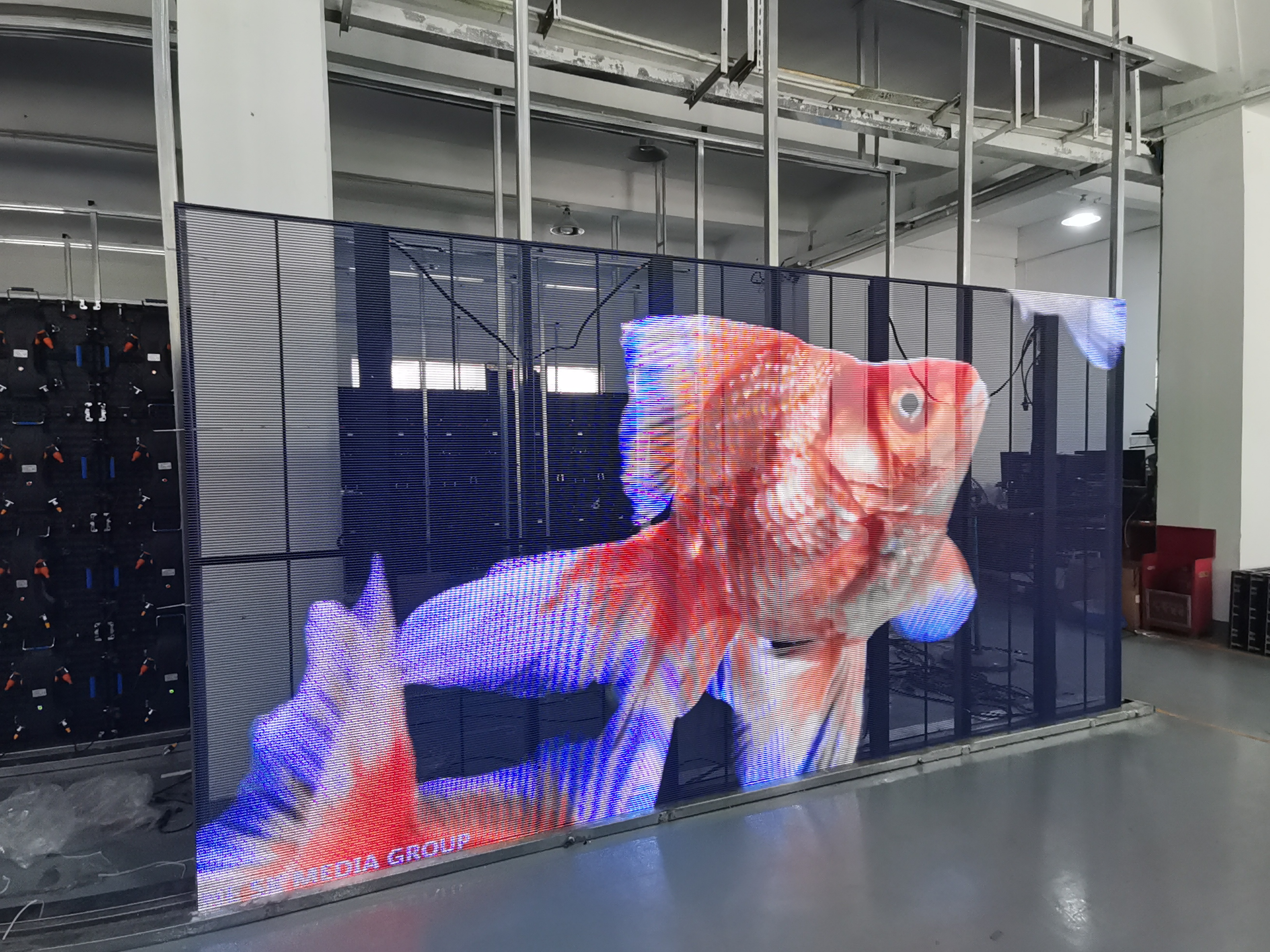
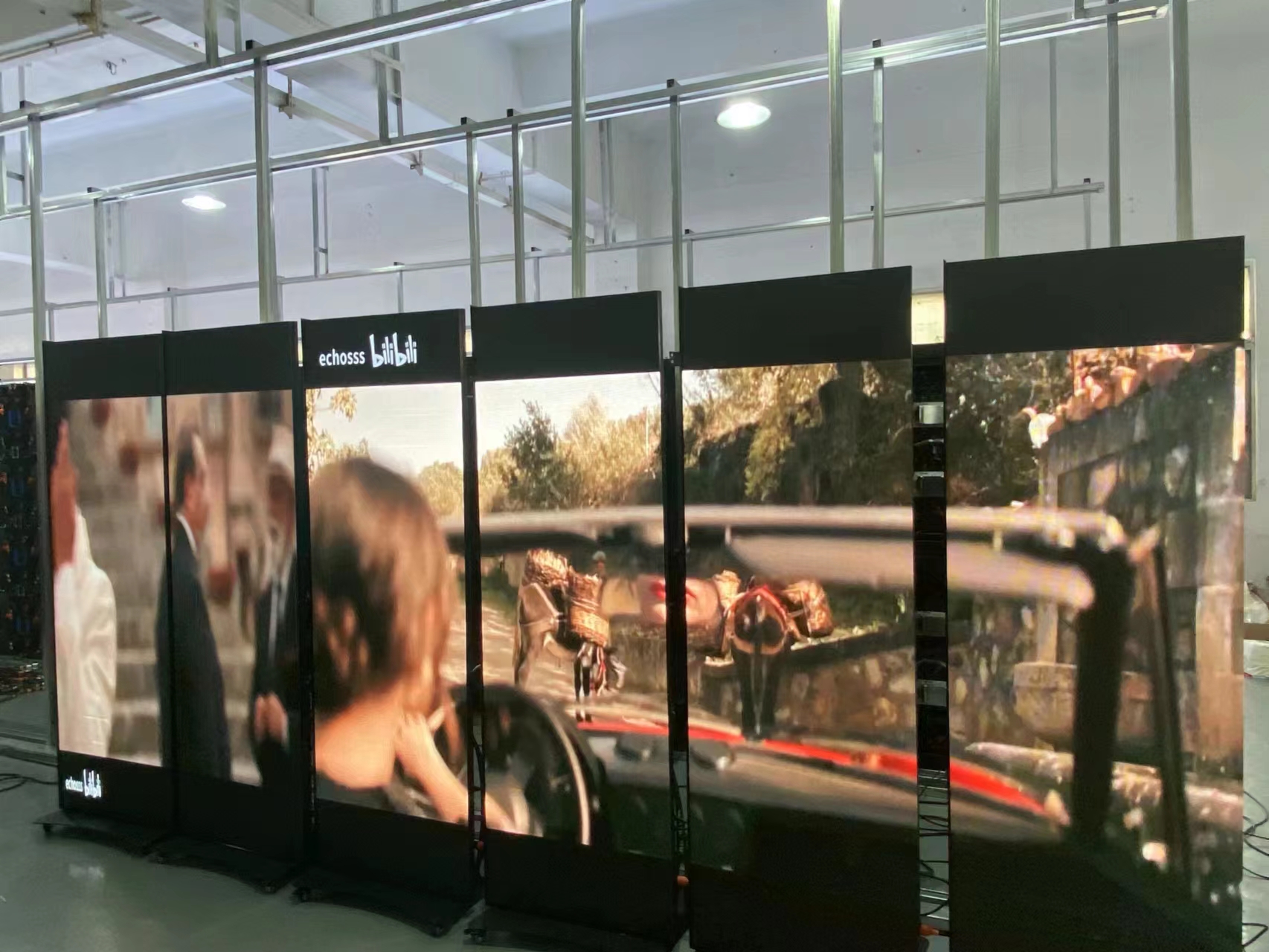
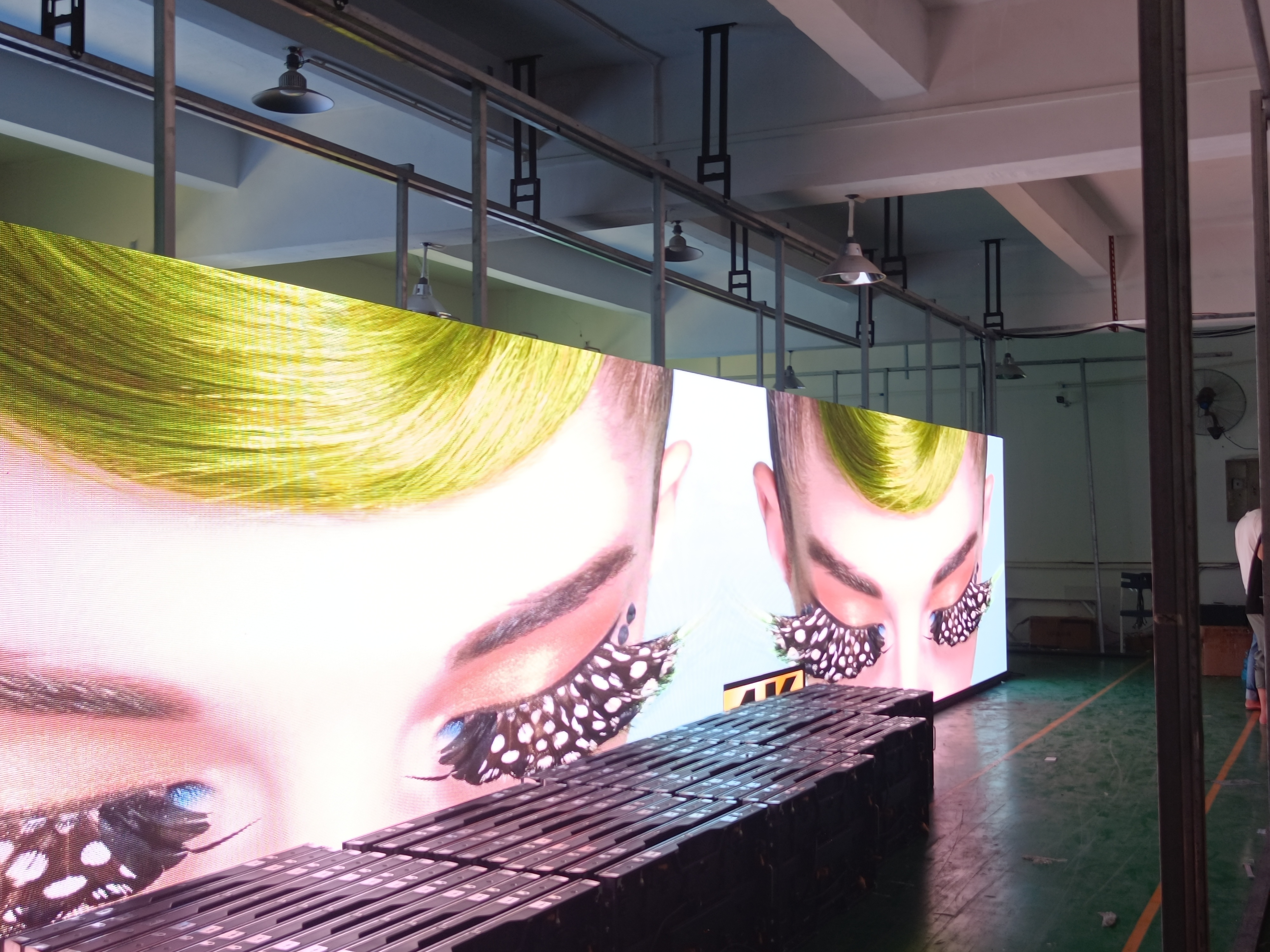
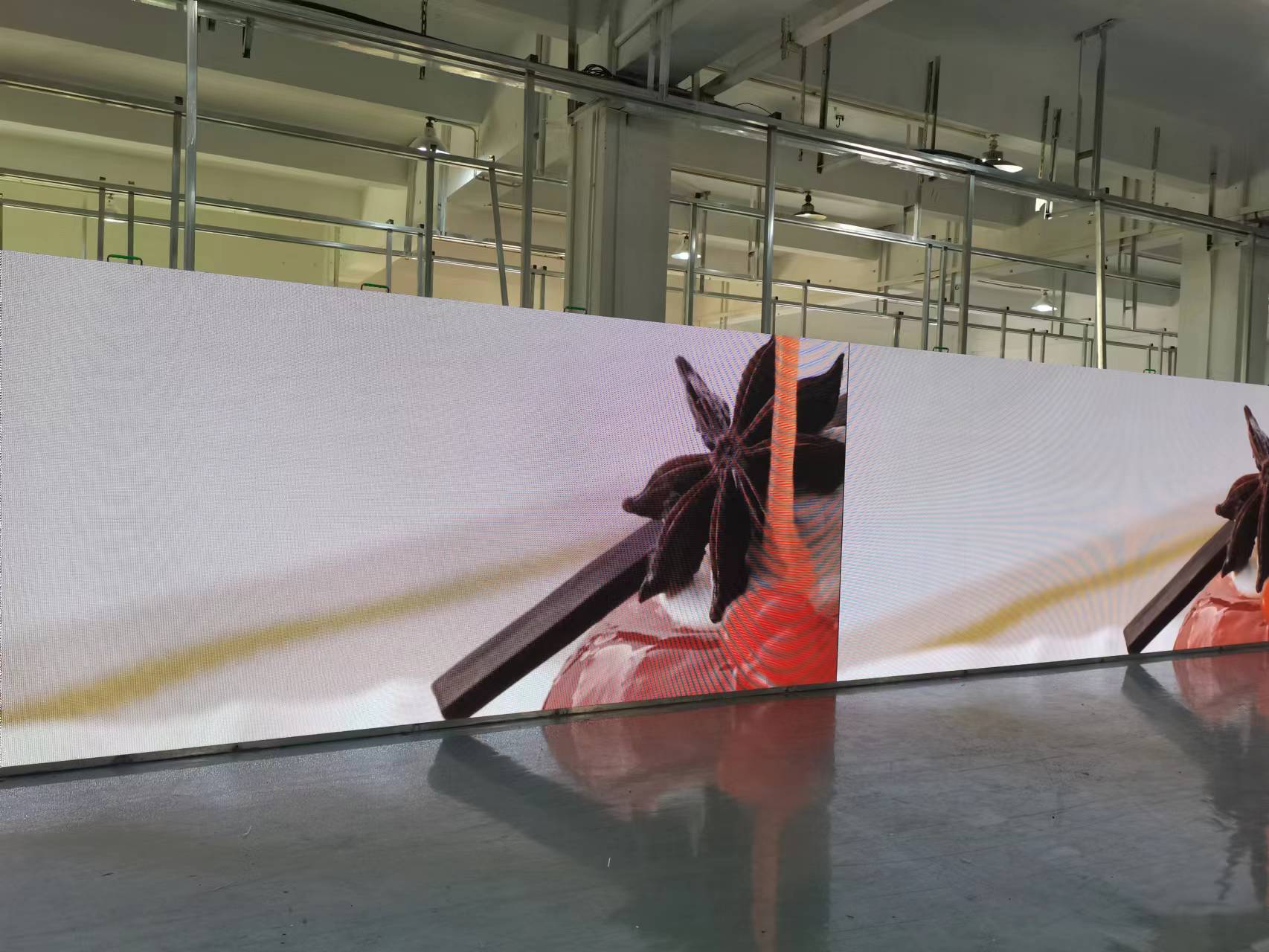
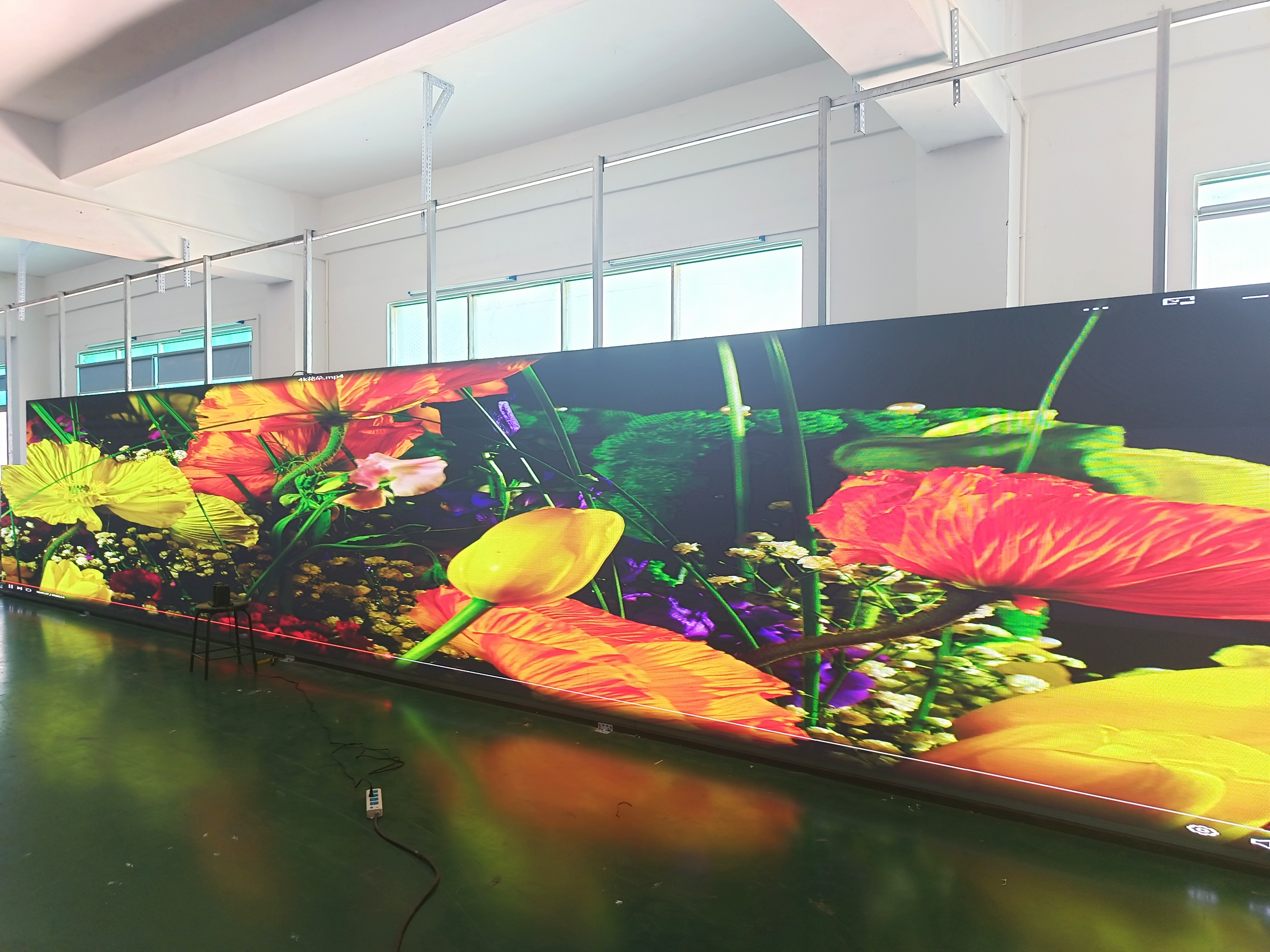
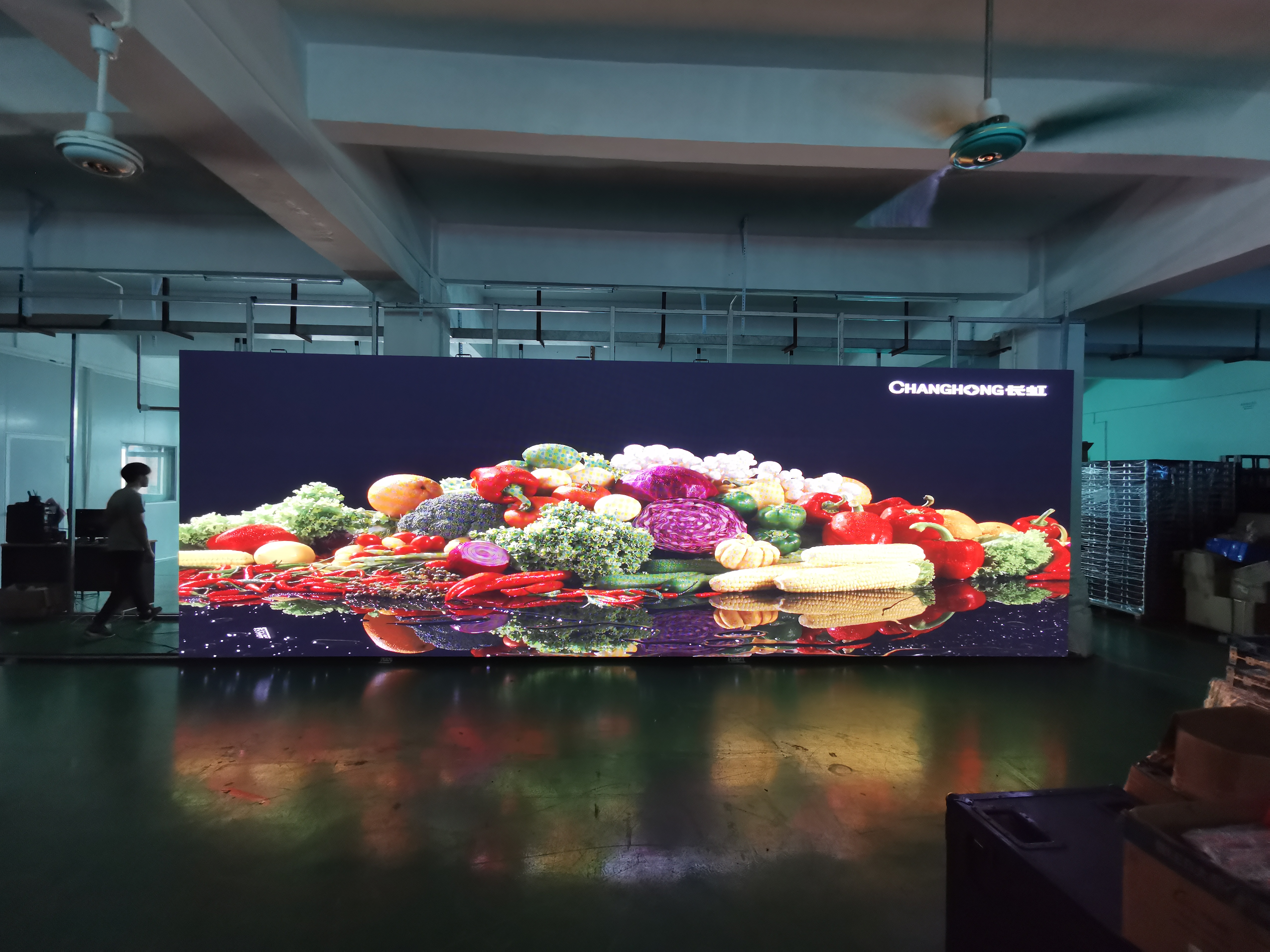
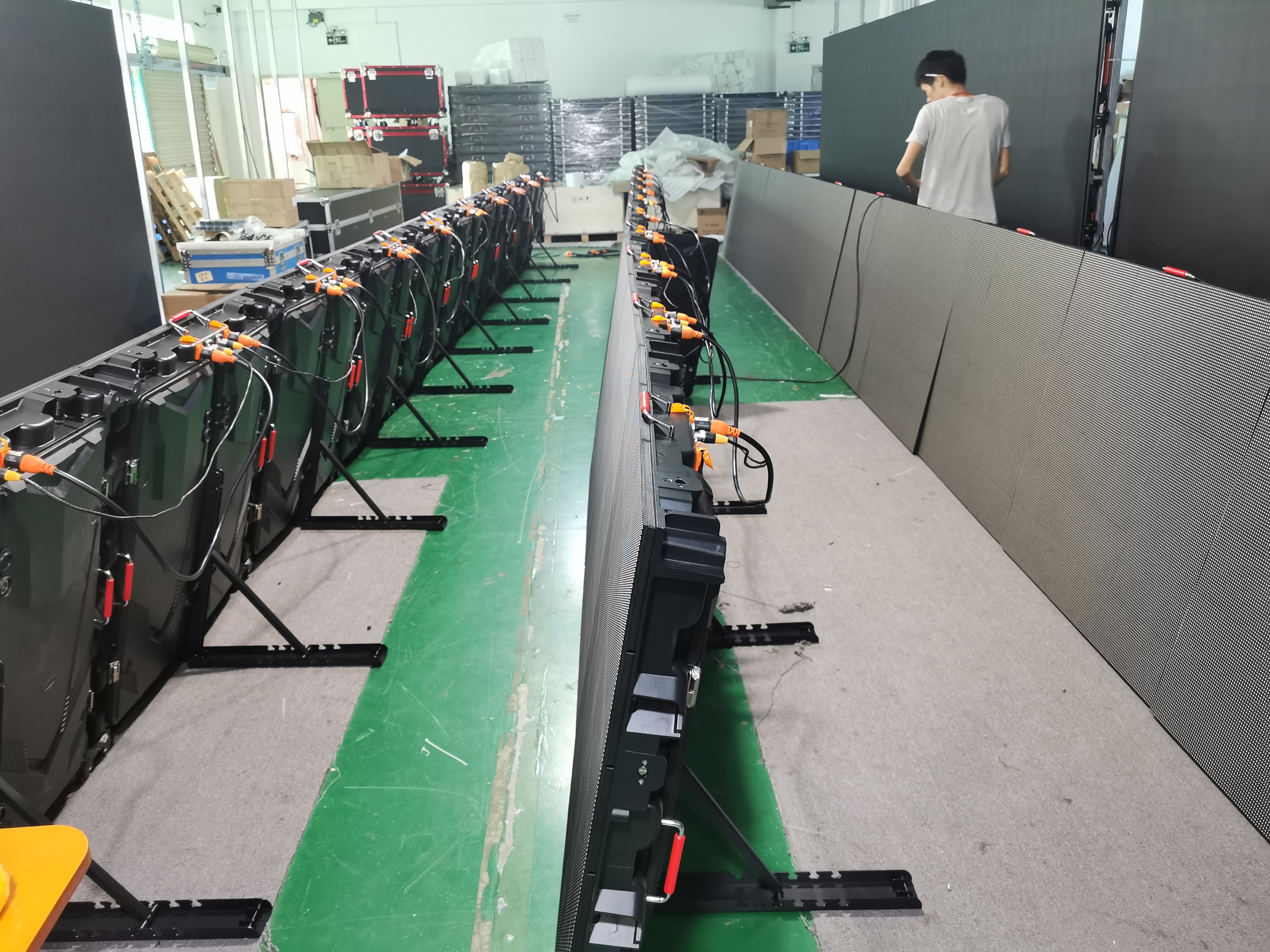
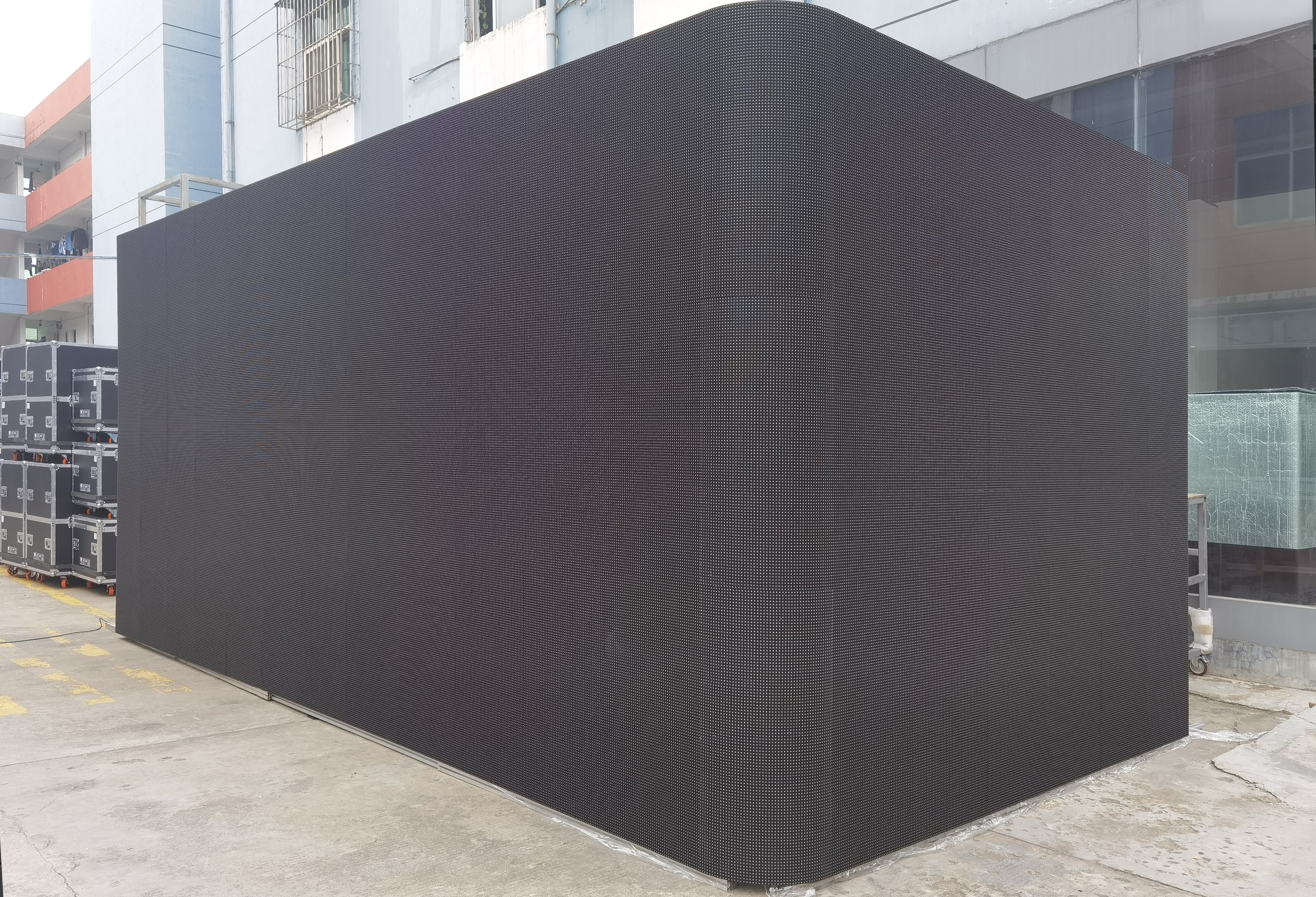